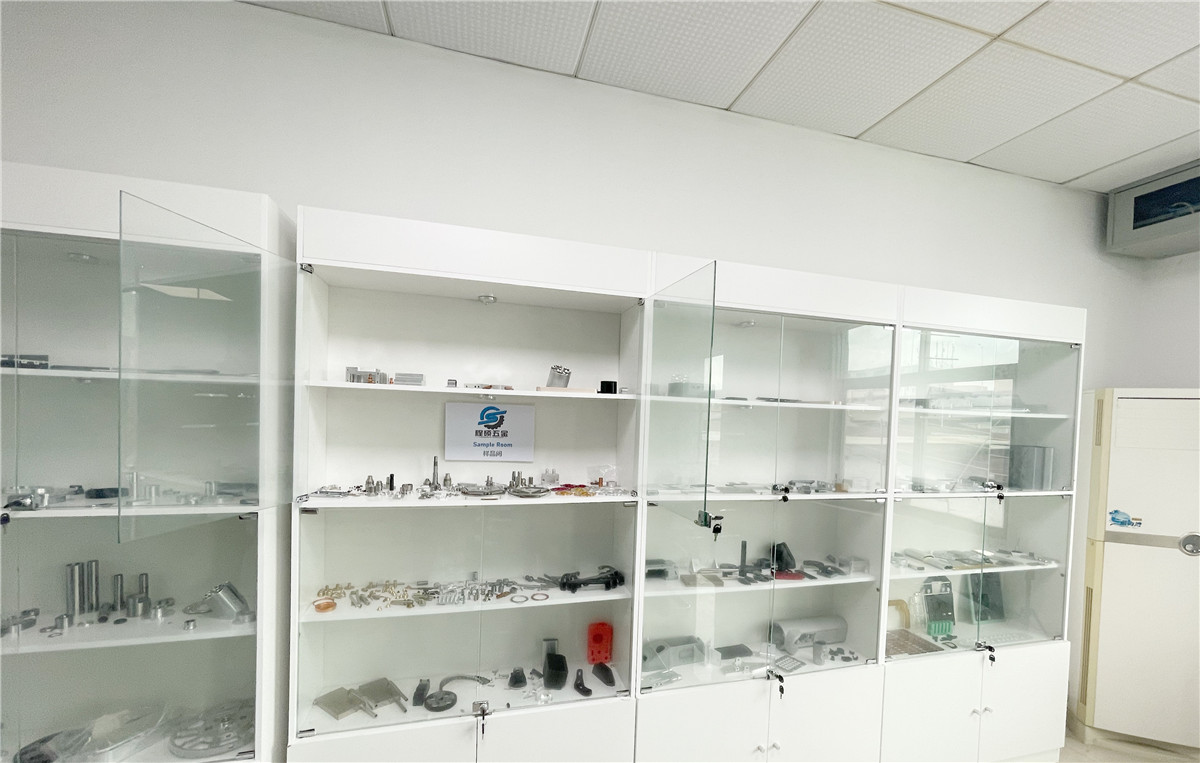
Chengshuo Hardware Samples Room
Title: CNC Industry Innovation Shaping the Future of Manufacturing
Introduction:
The Computer Numerical Control (CNC) industry is experiencing significant advancements that are revolutionizing the manufacturing sector. CNC systems, which utilize computer-aided design (CAD) and computer-aided manufacturing (CAM), have become essential in the production of a wide range of components with high precision and efficiency. This article highlights some recent developments and trends in the industry that are shaping the future of manufacturing.
1. Automation and Robotics:
Automation and robotics are transforming the CNC industry, making manufacturing processes more streamlined and efficient. The integration of robots with CNC machines enables continuous and unmanned production, minimizing human error and increasing productivity. With the implementation of artificial intelligence (AI) and machine learning, CNC programs can optimize production schedules and adapt to changing demands.
2. Additive Manufacturing (3D Printing):
Additive manufacturing, commonly known as 3D printing, is making significant strides in the CNC industry. This technology allows for the creation of complex geometries and intricate designs with utmost precision. The integration of CNC systems with 3D printing enables the production of customized parts and prototypes, reducing lead times and costs for manufacturers.
3. Internet of Things (IoT) and Big Data:
The CNC industry is embracing the Internet of Things (IoT) and big data analytics to enhance productivity and efficiency. CNC machines are now equipped with sensors that collect real-time data, enabling continuous monitoring of machine performance, maintenance, and energy consumption. Manufacturers can analyze this data to optimize production processes, reduce downtime, and make informed decisions.
4. Integration of Cloud Computing:
Cloud computing has revolutionized various industries, and the CNC industry is no exception. By storing and processing large amounts of data on the cloud, manufacturers can access CNC programs and designs remotely, greatly expanding collaboration possibilities. Additionally, cloud-based systems offer real-time monitoring of production processes, enabling manufacturers to make timely adjustments for improved efficiency.
5. Enhanced Cybersecurity Measures:
With increased connectivity, the CNC industry faces a higher risk of cyber threats. As a result, there is a growing focus on implementing robust cybersecurity measures to safeguard sensitive information and protect CNC systems from potential attacks. Encryption, firewalls, and user authentication protocols are being adopted to ensure the integrity and security of CNC operations.
6. Sustainable Manufacturing Practices:
The CNC industry is also making strides towards sustainable manufacturing practices. Efforts are being made to reduce energy consumption, minimize waste generation, and adopt environmentally friendly materials. CNC machines equipped with energy-efficient components and optimized cutting strategies are contributing to a greener manufacturing sector.
Conclusion:
The CNC industry continues to evolve rapidly, driven by technological advancements that are shaping the future of manufacturing. Automation, robotics, additive manufacturing, IoT, big data analytics, cloud computing, enhanced cybersecurity measures, and sustainable practices are reshaping the way components are produced. These innovations not only improve precision and efficiency but also enhance collaboration, reduce lead times, and contribute to a more sustainable manufacturing sector. As technology continues to advance, the CNC industry is poised to play a vital role in the fourth industrial revolution, driving economic growth and productivity on a global scale.
Post time: Nov-25-2023